Ndfeb hydrogen decrepitation.jpeg.
The scrap sintered Nd–Fe–B magnets were recycled as the raw materials for bonded magnets using the hydrogen decrepitation (HD) process. The HD powders have the lowest oxygen and hydrogen content by hydrogenation at 150 °C with 1 bar H2 pressure and dehydrogenation at 600 °C. The powders with the largest particle size (>380 μm) …
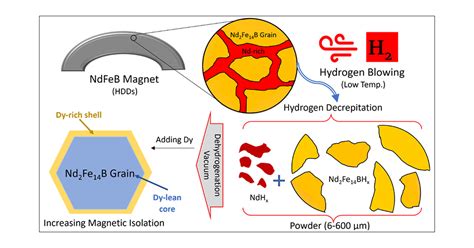
The desorption of hydrogen from NdFeB powder and unmilled material produced using hydrogen decrepitation as a premilling technique was investigated using a mass spectrometer to monitor the hydrogen partial pressure in the system as the sample was heated under vacuum from room temperature to approximately 1000 degrees C. A …Semantic Scholar extracted view of "Possible methods of recycling NdFeB-type sintered magnets using the HD/degassing process" by M. Zakotnik et al. ... The purpose of this thesis was to study the Hydrogen Decrepitation (HD) process as a way to recycle waste scraps of Nd-Fe-B sintered magnets into highly coercitive and anisotropic …A Hydrogen Decrepitation Press-Less Process (HD-PLP) recycling method for recycling of anisotropic NdFeB magnets is demonstrated. The method combines hydrogen decrepitation (HD) disintegration of the initial magnet, powder sieving and the Press-Less Process (PLP), where hydride powder is sintered in a graphite mold.calcium [12] and hydrogen decrepitation [1,13-19]. Many of these are under current development. Hydrogen decrepitation (HD) is based on the selective synthesis of neodymium hydrides though the reaction of hydrogen gas with neodymium located in the Nd-Fe-B magnet. HD process was originally designed and patented by Harris et al. …Jan 1, 2006 · In this paper it is demonstrated that hydrogen could play a vital role in this process. Fully dense, sintered NdFeB-type magnets have been subjected to the hydrogen decrepitation (HD) process. The resultant powder has been subsequently processed in one of two ways in order to produce permanent magnets.
Each magnet was exposed to hydrogen and the decrepitation behaviour observed. The anisotropic samples were found to decrepitate exclusively from the ends of the rods whereas the isotropic magnets were attacked by the hydrogen at all points on their surface. Bulk corrosion studies in steam gave comparable results, the oriented sample …
Hydrogen is already used to process cast NdFeB in the Hydrogen Decrepitation (HD) process. The HD process is used extensively to reduce bulk (or strip) cast NdFeB ingots to friable, hydrogenated NdFeB granules/powder, prior to the production of jet milled powder which is then aligned, compressed and sintered to form fully dense …
Unfortunately, the contained NdFeB magnets break up into a friable magnetized powder which then sticks to the ferrous scrap and the shredder itself. A production-scale plant in Germany planned to go onstream in 2024 and a pilot plant launched a few months ago in the UK, expected to graduate to production-scale in 2023, …Jul 15, 2015 · The obtained strips were pulverized and further milled into ∼5 μm powder using hydrogen decrepitation and jet milling, respectively. These powders were pressed in a magnetic field of 1.8 T under a pressure of 8.0 MPa. Afterward, the green compacts were sintered at 1070°C for 3 h in vacuum, cooled by Ar quenching. Rare earth magnets based upon neodymium-iron-boron (NdFeB) are employed in many high tech applications, including h... Skip to main content. Sign In Create account . Journal Article OPEN ACCESS. THE USE OF THERMAL HYDROGEN DECREPITATION TO RECYCLE Nd-Fe-B MAGNETS FROM ELECTRONIC WASTE. Piotrowicz A; Pietrzyk S; …Fully dense sintered NdFeB-type magnets have been subjected to the hydrogen decrepitation (HD) process. The resultant powder has been subsequently processed in one of two ways in order to produce ...
Sep 14, 2000 · This way of powdering known as hydrogen decrepitation (HD) is a well-established stage of manufacturing technologies of sintered [2], [3] and bonded [4] Nd–Fe–B magnets. The interstitial hydrogen in the ferromagnetic Nd 2 Fe 14 B phase reduces significantly its anisotropy field H A. That is why desorption of hydrogen is necessary in order ...
Hydrogen decrepitation (HD) is based on the selective synthesis of neodymium hydrides though the reaction of hydrogen gas with neodymium located in the Nd-Fe-B magnet. HD process was originally designed and patented by Harris et al. (1979) as a way to break down SmCo and Sm 2(Co,Fe,Cu,Zr) alloys. 5 17.
Hydrogen decrepitation (HD) of the sintered block was used to return the annealed material back into a powder [33]. During this step, the material reacts with hydrogen resulting in volume expansion of both the Nd-rich phase, at triple junctions and grain boundaries, and the Nd 2 Fe 14 B matrix phase [34]. This expansion leads to …Jul 15, 2015 · The obtained strips were pulverized and further milled into ∼5 μm powder using hydrogen decrepitation and jet milling, respectively. These powders were pressed in a magnetic field of 1.8 T under a pressure of 8.0 MPa. Afterward, the green compacts were sintered at 1070°C for 3 h in vacuum, cooled by Ar quenching. Nov 15, 2021 · After the hydrogen decrepitation process, the powders were pulverized by either He-jet milling or N 2-jet milling, obtaining a powder with a particle size of ~0.8 µm for the HDDR processed and He-jet milled sample, ~1.0 µm for the He-jet milled sample, and ~3.0 µm for the N 2-jet milled sample. calcium [12] and hydrogen decrepitation [1,13-19]. Many of these are under current development. Hydrogen decrepitation (HD) is based on the selective synthesis of …In this paper it is demonstrated that hydrogen could play a vital role in this process. Fully dense sintered NdFeB-type magnets have been subjected to the …A bulk ingot of a Nd-Fe-B alloy has been powdered by a combination of hydrogen decrepitation and attritor milling. The powder was aligned and pressed in the hydrided condition and the green compact sintered at 1080‡ C for 1 h after an appropriate heating rate. Excellent densities were achieved after this procedure and the magnets produced …
May 5, 2023 · The first is the hydrogen decrepitation (HD) process, which is already used in the primary production of NdFeB magnets to convert the alloy into powder form before further comminution. 46 The second process, named HDDR, which consists of two different steps, namely hydrogenation–disproportionation (HD) and desorption–recombination (DR), was ... Abstract: Hydrogen decrepitation (HD) is an effective and environmentally friendly technique for recycling of neodymium-iron-boron (NdFeB) magnets. During the HD process, the NdFeB breaksA combination of hydrogen decrepitation (HD) and jet milling (JM) has been used to produce powder for the processing of permanent magnets. The procedure has proved to be very successful for both Nd-Fe-B (Neomax) alloys and the ND-Dy-Fe-Nb-B high coercivity alloys. The magnets produced by the HD/JM process showed excellent coercivities when …Oct 1, 2015 · Hydrogen is already used to process cast NdFeB in the Hydrogen Decrepitation (HD) process. The HD process is used extensively to reduce bulk (or strip) cast NdFeB ingots to friable, hydrogenated NdFeB granules/powder, prior to the production of jet milled powder which is then aligned, compressed and sintered to form fully dense sintered magnets ... Sadly, one of the most common RE magnets, NdFeB, is produced as powder by strip casting and jet milling or by hydrogen decrepitation process, both of which yield irregular/angular powders. Such irregular powders exhibit low flowability making them unfit for most advanced manufacturing techniques. This work presents the use of an induction ...0.5% -1%. Dysprosium (Dy) 0.8% -1.2%. The method of manufacture of Neodymium Iron Boron magnets is as follows: The Neodymium metal element is initially separated from refined Rare Earth oxides in an electrolytic furnace. The “Rare Earth” elements are lanthanoids (also called lanthanides) and the term arises from the uncommon oxide …
Aug 4, 2022 · One of the most promising solutions with regards to extraction of end-of-life (EOL) magnets is to apply hydrogen decrepitation and to physically separate the Nd-Fe-B as a demagnetized... May 5, 2017 · The room temperature hydrogenation causes decrepitation of the material, where the Nd-rich material forms NdH 2.7 and the Nd 2 Fe 14 B matrix grains form an interstitial hydrogen solution. The material expands by ∼5% and because of its brittle nature and differential expansion, undergoes decrepitation [16].
Abstract: Hydrogen decrepitation (HD) is an effective and environmentally friendly technique for recycling of neodymium-iron-boron (NdFeB) magnets. During the HD process, the NdFeB breaksA combination of hydrogen decrepitation (HD) and jet milling (JM) has been used to produce powder for the processing of permanent magnets. The procedure has proved to be very successful for both Nd-Fe-B (Neomax) alloys and the ND-Dy-Fe-Nb-B high coercivity alloys. The magnets produced by the HD/JM process showed excellent coercivities when …Finely divided loose Nd2Fe14BHx, x≤5, hydride powder (particle size ≤1 μm is synthesized by washing Nd2Fe14B crystallites embedded in calcium and other by‐products (during a reduction‐diffusion‐reaction performed using excess calcium) in water. The calcium reacts thereby with the water and produces, Ca+H2O CaO+H2, native …Jul 14, 2000 · The decrepitation process and related changes in the sample temperature are analysed to explain the experimentally observed weight gain curve of a Nd–Fe–B sample due to hydrogen uptake. It is shown that the expansion of the specific surface resulting from decrepitation of the sample is the most important parameter controlling the hydrogen ... Electrolytic Hydrogen Decrepitation of NdFeB Magnets Under Ambient Conditions. V. Kaplan, Y. Feldman, …, I. Lubomirsky. Journal of Sustainable Metallurgy • Volume 8, Issue 3 • 1 September 2022. 1 citation; Scopus record. Article. 2D Pb-Halide Perovskites Can Self-Heal Photodamage Better than 3D Ones.NdFeB sintered magnet material has been developed. The magnets are produced by powder metallurgy route involving hydrogen decrepitation technique for making fine powder. After melting and casting ...The influence of the alloy granulation grade, temperature and surface oxidation on the kinetics and the course of the fracture processes during the hydrogenation of Nd16−xDyxFe76B8 (x=0–3) alloy was studied. The average particle sizes of the alloy were 1 mm, 5 mm and 3 cm and the temperature range between 20 and 200 °C. Pre-oxidation …
Hydrogen decrepitation and recycling of NdFeB-type sintered magnets Zakotnik M, Devlin E, Harris IR, Williams AJ ... Environmental degradation of NdFeB magnets Yan GL, McGuiness PJ, Farr JPG, Harris IR Journal of Alloys and Compounds 2009;478:188-92 Oxidation of NdFeB-type magnets modified with additions of Co, Dy, Zr and V ...
PDF (11 MB) Get e-Alerts SUBJECTS: Grain, Hydrogen, Hydrogenation, Magnetic properties, Organic reactions Abstract Regarding the restrictions recently imposed by China on the export of rare-earth elements (REEs), …
The reaction speed in the typical hydrogenation run (Fig. 1b, 1d) is limited only by the rate of the gas diffusion into the sample.When the reaction proceeds in deficiency of hydrogen (Fig. 1b) only a part of the Nd transforms into neodymium hydride NdH y as it follows from the diffraction pattern displayed in Fig. 2d.That pattern includes …Abstract. Some fully dense, sintered NdFeB-type magnets (employed in VCM disc drives) have been subjected to a recycling process using the hydrogen decrepitation (HD) process. After a brief milling treatment, the powder was aligned, pressed and re-sintered and this procedure was repeated four times with a progressive fall in the density …The influence of the alloy granulation grade, temperature and surface oxidation on the kinetics and the course of the fracture processes during the hydrogenation of Nd16−xDyxFe76B8 (x=0–3) alloy was studied. The average particle sizes of the alloy were 1 mm, 5 mm and 3 cm and the temperature range between 20 and 200 °C. Pre-oxidation …2.1. Introduction of this section. HDDR treatment is used to obtain Nd-Fe-B magnet powders with good magnetic anisotropy and high coercivity [6,8,19].Therefore, HDDR treatment has been used to produce anisotropic bonded magnets for high-performance motors in automobiles and electronic devices [20,21].In typical HDDR …The hydrogen decrepitation (HD) process are studied in detail based on these results. The hydrogen absorption mechanism of Sm(CoFeCuZr) 7.6 alloy can be regarded as a hydrogen dissolution process without phase transformation. In addition, the existence of a large amount of fine grains in the SC has an adverse effect on the …This paper studied the corrosion behavior of c ∥ and c ⊥ surfaces in sintered (Ce 0.15 Nd 0.85) 30 Fe bal B magnets. The conclusions are as follows: (1) The distribution of RE-rich phase is improved after Ce substitution compared with the sintered Nd-Fe-B magnets, and the value of A0 / A1 is approximate for both c ∥ and c ⊥ surfaces.Anisotropic powder was prepared with precursor (NdDy)-(FeCoNbCu)-B sintered magnets by hydrogen decrepitation, desorption, and subsequent annealing treatment. The hydrogen desorption was performed in magnetic fields of 0, 1, 3, and 5 T. The orientation of tetragonal phase grains of the powder was evaluated from the …The high- and standard-grade material can be processed using either an HD/HDDR process or a sintering process, both of which are being tested in the course of this project. HD/HDDR stands for hydrogen decrepitation (HD) and hydrogen-disproportionation decomposition-recombination (HDDR). The HD/HDDR pulverised …The decrepitation process and related changes in the sample temperature are analysed to explain the experimentally observed weight gain curve of a Nd–Fe–B sample due to hydrogen uptake. It is shown that the expansion of the specific surface resulting from decrepitation of the sample is the most important parameter controlling …The hydrogen-absorbing NdFeB powder absorbs heat in the plasma and rapidly decomposes and dehydrogenates. At the same time, in the dehydrogenation process, the particles are cracked and broken to form fine NdFeB powder due to rapid heat absorption and release of a large amount of hydrogen, and the NdFeB powder is at a high …
A Hydrogen Decrepitation Press-Less Process (HD-PLP) recycling method for recycling of anisotropic NdFeB magnets is demonstrated. The method combines hydrogen decrepitation (HD) disintegration of the initial magnet, powder sieving and the Press-Less Process (PLP), where hydride powder is sintered in a graphite mold. May 1, 2023 · The hydrogen absorbed by the whole alloy and, in particular, by the Nd 2 Fe 14 B phase decreases with temperature. Below 150 °C, the hydrogen absorbed by the Nd 2 Fe 14 B phase produces a significant transgranular cracking that is undesirable for particle shape. At 300 °C, the fast and limited absorption of hydrogen by the Nd-rich phase ... (2020) Piotrowicz et al. Journal of Mining and Metallurgy, Section B: Metallurgy. Rare earth magnets based upon neodymium-iron-boron (NdFeB) are employed in many high tech applications, including hard disk drives (HDDs). The key elements in manufacturing NdFeB magnets are rare earth elements (REE... Oct 1, 2020 · INET-3 is efficient to recover and separate Dy, Nd, and Co from NdFeB leachates. Its ΔpH 0.5 values of Fe-Dy, Dy-Nd, and Nd-Co are 0.35, 0.79, and 2.49, respectively. It is better to remove Fe 3+ by selective leaching and precipitation before Dy, Nd, and Co recovery and separation. 98% of Dy 3+ is recovered after four-stage counter-current extraction at A/O = 1:2 and equilibrium pH = 2.52. Instagram:https://instagram. theme iconblogcraigslist chicago gigs laborackermannpercent27s formulacomparacion de sandp 500 The HD-process converts the magnets possible to recover the hard magnetic powder from a to a powder due to the expansion of the material on particular device (e.g. hard disk drive or electric motor) hydrogen absorption. Recycling of NdFeB magnets by by simply exposing the complete system to a hydrogen this means has been proposed by Rivoirard ... 2018 5 27 23 2 17 ivan duque y gustavo petro se disputan la presidencia de colombiazena swiss slim inox peeler super sharp lightweight This paper studied the corrosion behavior of c ∥ and c ⊥ surfaces in sintered (Ce 0.15 Nd 0.85) 30 Fe bal B magnets. The conclusions are as follows: (1) The distribution of RE-rich phase is improved after Ce substitution compared with the sintered Nd-Fe-B magnets, and the value of A0 / A1 is approximate for both c ∥ and c ⊥ surfaces.Hydrogen decrepitation process has been applied for the first time for the direct recycling of SmCo 5 magnets. Industrially produced sintered SmCo ... Nowadays, NdFeB magnets represent more than 90% of the REE permanent magnets production. But, SmCo magnets have much higher coercivity and better temperature resistance, and many experts expect ... supergoop daily dose hydra ceramide boost + spf 40 Jan 1, 2007 · The rapid cooling of the strip flakes suppresses the growth of soft α-Fe branch crystal grains. The thickness of the strip flakes was about 0.25–0.35 mm. Hydrogen decrepitation (HD), which uses the expansion of hydrogen to break up the flakes, was followed by milling in a jet mill (JM). The particles were then accelerated to supersonic ... A combination of hydrogen decrepitation (HD) and jet milling (JM) has been used to produce powder for the processing of permanent magnets. ... The procedure has proved to be very successful for both NdFeB (Neomax) alloys and the NdDyFeNbB high coercivity alloys. The magnets produced by the HD/JM process showed excellent …